What key points should be followed in the selection of gear production materials?
/in News /by adminThe most important thing in gear production process is to select good materials. Only with good materials can we produce high quality gears. For the selection of materials, the main points are as follows:
1. Meet the technological performance of gear material
The technological properties of materials refer to the ability of materials themselves to meet various processing requirements. Gears are manufactured by forging, cutting and heat treatment. Therefore, attention should be paid to the technological properties of materials when selecting materials.
2. Economic Requirements of Materials
On the premise of satisfying the service performance, the selection of gear production materials should also pay attention to reducing the total cost of parts as far as possible. Consider the price of the material itself. Carbon steel and cast iron are relatively cheap, so choosing carbon steel and cast iron on the premise of meeting the mechanical properties of parts not only has better processing performance, but also can reduce costs. Consider the cost of gear production process. Firstly, different heat treatment methods have different relative processing costs. Secondly, the cost can also be reduced by improving the heat treatment process.
3. Rational Selection of Gear Production Materials
To satisfy the mechanical properties of the material, the root of the tooth is subjected to large bending stress, which may cause strength failure of the tooth surface or the tooth body. Relative sliding occurs at all points of the tooth surface, resulting in wear and tear. The main failure modes of gears are tooth surface erosion, tooth surface gluing, tooth surface plastic deformation and tooth fracture.
Therefore, gear production materials are required to have high bending fatigue strength and contact fatigue strength, sufficient hardness and wear resistance of the tooth surface, and certain strength and toughness of the core.
Luoyang primary precision equipment co.,Ltd is a professional manufacturer of gears and gear shafts. We can customize all kinds of gears and gear shafts according to the material and technical requirements of customers.
Ball mill pinion
/in News /by adminPinion gear is one of the indispensable spare parts of ball mill equipment, according to the direction of tooth shape can be divided into straight teeth and oblique teeth, there are two kinds of key type and expansion type. Different specifications of the ball mill selection of pinion teeth and modulus are not the same. Mainly according to the speed of the mill and the bearing capacity of the gear itself. Regardless of the type of ball mill, the quality of the pinion is of great importance, which directly affects the operation and service life of the equipment.
Ball mill pinion material hardness:
The gears are forged with ZG45#, 35SiMn, 45MnB, 40Cr and other materials according to customer requirement and drawing, and the hardness can reach HRC40-55 through tempering. Mechanical properties of pinion or shaft gear materials should not be lower than the relevant provisions, tooth surface hardness should be higher than the hardness of big gear tooth surface 30HB above, machining accuracy should meet GB/T 10095.
Specification selection of pinion for ball mill:
General situation 1.5, 183, 2.2 meters ball mill is the national standard configuration, gear ring(gear rim) specifications are unified, the rest of the ball mill for non-standard products, manufacturers if need to replace pinion accessories, must know the gear modulus, tooth number and external diameter, internal diameter, stop, displacement coefficient and other data. It is better to have the drawing provided by the mill manufacturer. If there is no drawing, please find a professional to accurately measure the above data and draw a sketch. Provide customized check data to qualified manufacturers.
Pinion module of ball mill:
Module is the ratio of pitch t to PI (m = t/ PI) between the teeth of the same side of two adjacent gears, measured in millimeters. Modulus is one of the most basic parameters in gear manufacturing. The larger the modulus is, the higher the tooth is, the thicker the tooth is. National standard ball mill pinion module is not less than 14, commonly used gear module is 18 module, 20 module, 22 module, 24 module, 25 module, 26 module, 28 module, 30 module. The number of teeth and modulus of gears are set according to the requirements of mechanical and mechanical principles.
Design of pinion for ball mill:
There is a minimum number of teeth, is to prevent in the hobbing root cutting phenomenon. Pinion generally must not be less than 17 teeth, pinion number is usually designed for singular, large gear is generally haff-type split structure of the number of teeth for even, and paired with the number of large gear teeth best prime, at least can not be integral multiples of each other, so as to avoid serious local tooth wear phenomenon. So it’s important to determine the transmission ratio. Balance the relation between the number of teeth and modulus according to center distance and transmission ratio.
Pinion tooth structure of ball mill:
Generally divided into two types, one is involute cylindrical spur gear, the other is helical cylindrical gear. Matching gear along the tooth width at the same time into meshing, easy to produce vibration noise, transmission is not smooth. Helical cylindrical gear is better than cylindrical spur gear in grinding machine, and can be used for high speed and heavy load. However, because the manufacturing cost of helical cylindrical gears is much higher than that of cylindrical spur gears, most pinion gears of ball mill on the market are cylindrical spur gears. Pinion and pinion shaft are usually connected in the form of expansion and internal keys.
Price of ball mill pinion:
There are many factors that determine the price of pinion gear. If the pinion gear of the same specification is made of different materials, different manufacturers and different regions, the final price will be different. Mainly is the pinion material and blank weight, followed by the specific requirements and the tedious degree of gear processing.The pinion gears of ball mill manufactured by our factory are all processed by hobbing teeth or grinding teeth, the accuarcy of teeth can up to ISO6, and the tooth surface is quenched with high frequency.
Ball mill pinion scope of supply:
We can manufacture pinion for cement ball mill pinion pinion slag ball mill, ball mill pinion of fly ash, high fine grinding machine pinion, pinion bearing ball mill, sand ball mill pinion, wet ball mill pinion, gypsum ball mill pinion, the overflow type ball mill pinion, ceramic ball mill pinion, dressing ball mill pinion, the grid mill pinion, desulfurization ball mill pinion, the wind sweep gear grinding machine, drying coal power plant coal ball mill grinding pinion, rod mill pinion and so on.
What is the difference between casting and forging?
/in News /by adminCastings is used for a wide range of wearparts and components that are too large, complicated, intricate or otherwise unsuitable for the forging process. We can machine casting parts up to 50Tons.
No real upper size limit in casting weight
Large range of alloy choices
As forgings remain solid, custom alloys are far more difficult to get into production whereas with casting, alloys including Chrome, Nickel and Moly can be added at the molten stage.
Tooling is often less expensive than forge dies
Smaller production “runs” required
Complicated/complex parts are no problem
For large and complex components – casting is a fantastic method of manufacture.
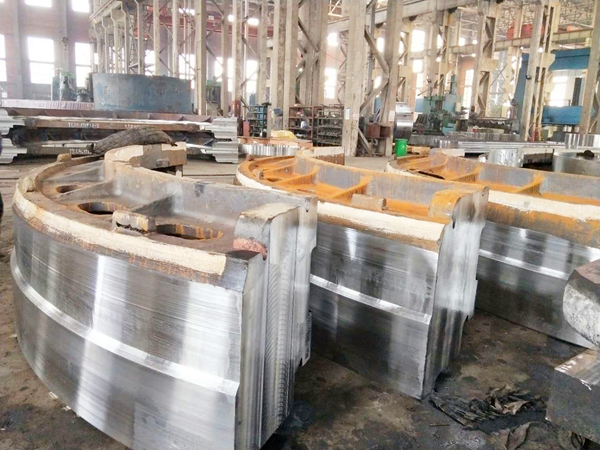
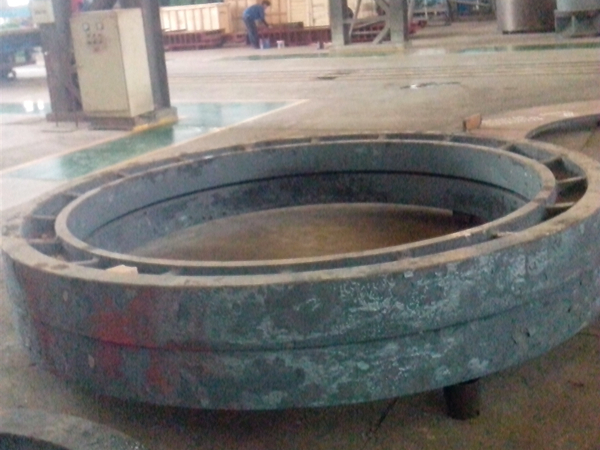
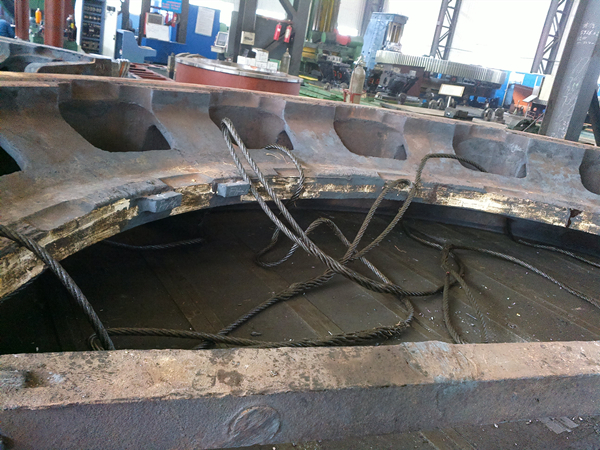
Forging offers uniformity of composition and structure. Forging results in metallurgical recrystalisation and grain
refinement as a result of the thermal cycle and deformation process. This strengthens the resulting steel product particularly in terms of impact and shear strength.
Generally tougher than alternatives
Will handle impact better than castings
The nature of forging excludes the occurence of porosity, shrinkage, cavities and cold pour issues.
The tight grain structure of forgings making it mechanically strong. There is less need for expensive alloys to attain high strength components.
The tight grain structure offers great wear resistance.
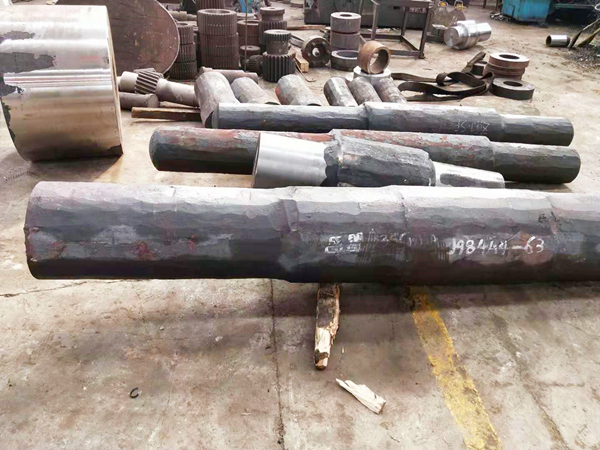
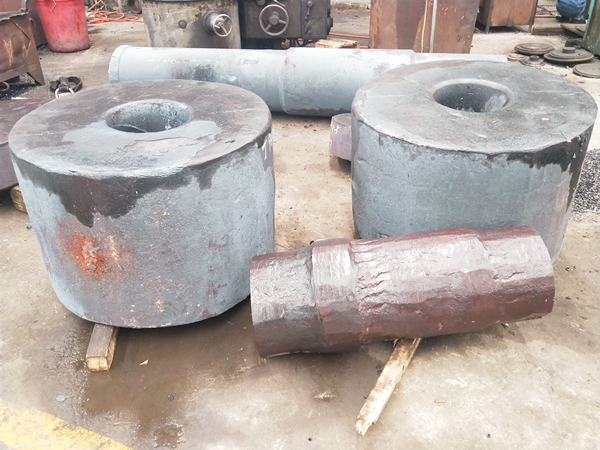
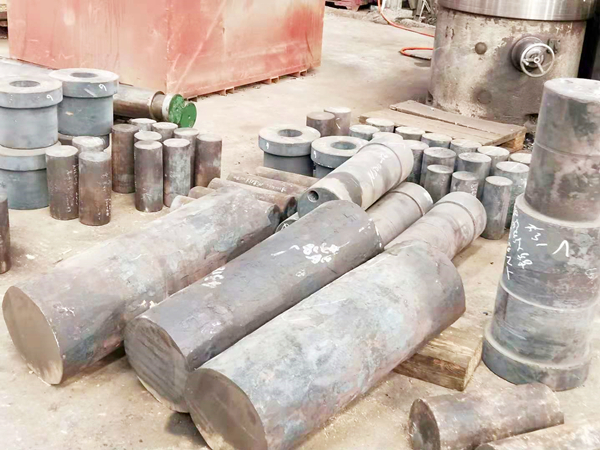
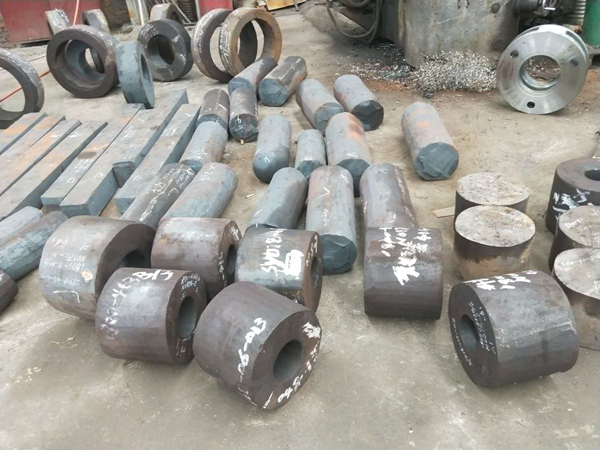
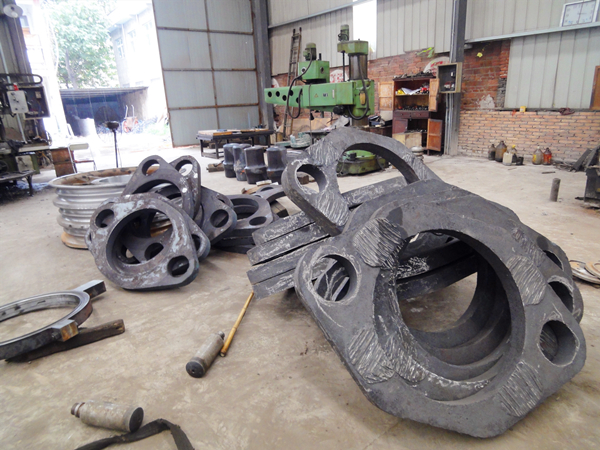
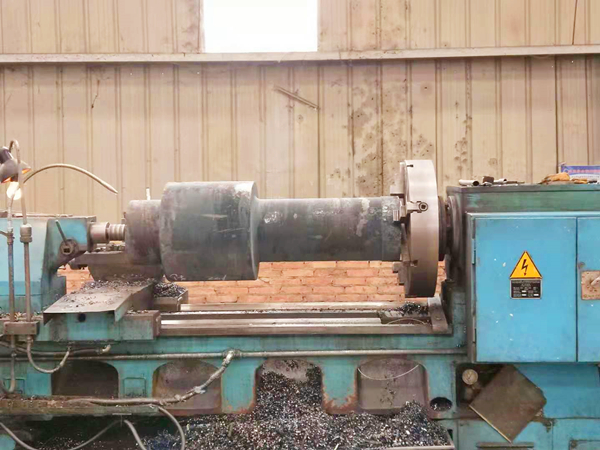
M25 T21 DIN18CrNiMo7 ball mill pinion(forged pinion shaft) shipped to Russia.
/in News /by adminPRM finished producing the pinion shaft within two months, and transported to Shanghai port.
CZ customer visited and built cooperation with PRM.
/in News /by adminThis customer was found by our company’s foreign trade personnel through Internet search at the end of June. After communication by email and Whatsapp, we made two quotations for spur gear, spiral bevel gear and ball mill gear sent by the customer. He was very satisfied with the price and details provided. We received the customer’s formal order soon, and our staff also sent the 5000mm spline shaft under production to the customer at this time. Customer was very interested and immediately said he would visit our company.
Customer come to our company on July 08 as scheduled, customer visited our forging workshop, gear, gear shaft processing workshops, spiral bevel gear processing workshops with accompany of our staff, our engineer introduced luoyang machining status, our production process, quality control, process capability, etc., customer satisfied all of the details.
The customer is very satisfied with the measurement and comparison of the sizes of the actual products produced by our company and the sizes of the drawings, indicating that we can cooperate with more and more cases in the future.
◎What we do:
PRM offers you complete in-house design and custom gearbox manufacturing services, also with repair and upgrade service.
We also provide customized gears and shafts according to customer’s technical requirement and drawing, along with product as below.
Gear wheel, spur gear, helical gear, bevel gear, worm and worm gear,shaft, gearshaft, girth gear/gear rim, industrial gearbox, gear reducer, housing, roller, gear coupling, rotary kiln belt, support roller, roller shell, ball mill end cover, ball mill girth gear, casting, forging, welding and other different spare parts for heavy duty industrial
◎Why US:
20 years experience;
Strong design and technical ability;
Variety of complete equipment and test instrument;
Strict produce process and inspection;
Fast delivery and resonable price;
7*24 hours online and timely reaction with satisfying solution.
Wish we can be partner.
Application of gear shaft in design
/in News /by admin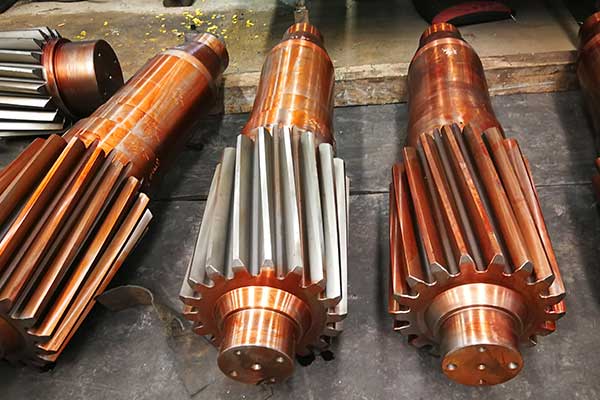
In the usual design, the gear shaft is generally used in the following situations:
Generally gear shaft is a pinion (less teeth gear)
Gearshaft is in the high speed level (low torque level)
the gear shaft is rarely used as a speed sliding gear, generally are fixed running gear, because it is not suitable for sliding speed in the high-speed level.
gear shaft is shaft and gear synthesis as a whole, but, in the design, we need to shorten the length of the shaft, it is not easy to hobbing if the forging shaft is too long, and it would increase the strength (such as rigidity, deflection, bending) with long support.
We can produce forging pinion, gearshaft with max length 15000mm and max diameter 3000mm.
Ball mill running model was delivered to Kluber Lubrication and received highly thanks and praised.
/in News /by adminThe ball mill operation Model was designed and produced by PRM deliver to Kluber lubrication, and received customer thanks and praise.
This ball mill model will be used at exhibition to promote the lubricants. It took just a month only from understanding customer needs, design, production and finish it. Customer is very satisfied with the design, delivery, service, package and etc. Kluber person said that he has never seen such a company do the details well, and they will certainly to cooperate with us again.
Kluber lubricants is the world’s leading manufacturer of specialty lubricants for oems. The company provides intelligent friction solutions and sells a variety of customized special lubricants directly to almost all industries and markets.
We have strong design capabilities and technical support in industrial gearboxes and related industries, please contact us for more details.
What is 0 degree spiral bevel gear?
/in News /by adminIn general, bevel gear is with spiral angle 35 degree.
But there is a special bevel gear with spiral angle 0 degree. So it called 0 degree spiral bevel gear.
Its shape is similar to straight bevel gear, but with higher strength, lower noise, and 0 degree spiral bevel gear is also with higher accuracy since it can be processed gear grinding.
Contact us
Address: Industrial Park In Science And Technology, Jianxi District, Luoyang City, Hennan Province, China
Email: perry@prmdrive.com
Tel: +86 379 60606008,
Fax: +86 379 60606008
Mobile: +86 13949244876